
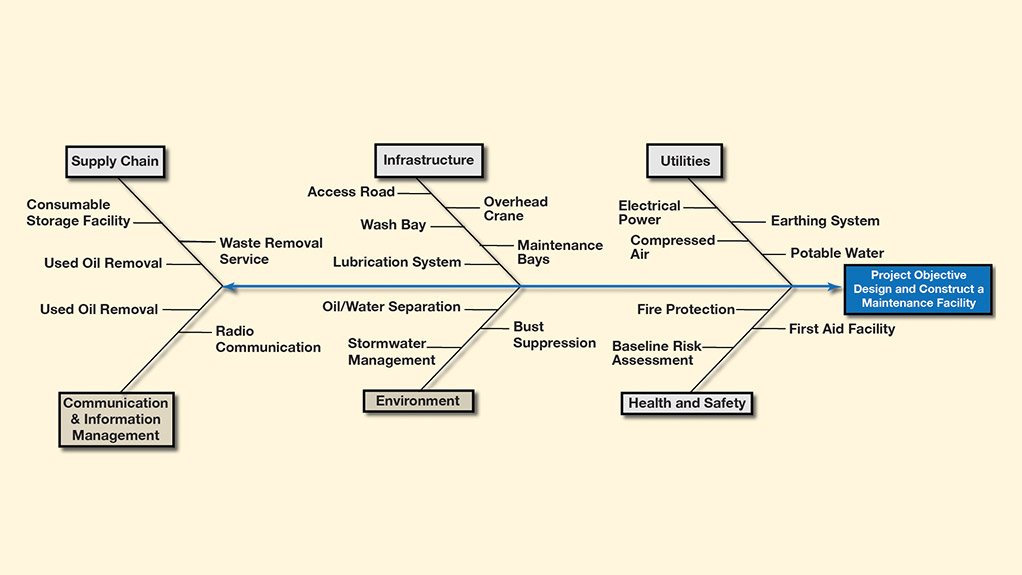
Possible causes of variation may be numerous, but they will invariably fall into the following categories:
ISHIKAWA DIAGRAM METHOD HOW TO
They allow you to make your plans so that you know how to deal with them in such a way that the quality of your final product is still up to standard and without significant variation. Variation in the process will mean variation in the product.įishbone diagrams help you to determine the variables that may enter the equation. From the moment your client contacts you, a predictable process should be followed with its aim being complete customer satisfaction. Whatever your business is, you don’t want to leave anything up to chance. When it comes to quality and efficiency, variation is your enemy.
ISHIKAWA DIAGRAM METHOD DRIVER
Even details such as designing the sportscar’s doors so that the driver could rest his arm on it while driving was taken into account. The iconic Mazda Miata car was designed to overcome the issues identified in a fishbone diagram. In the 1920s it was seen as an important quality control tool. Even back in the 60s, the fishbone diagram wasn’t anything new.
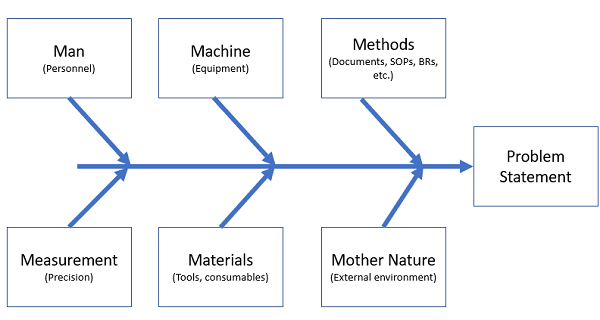
Karou Ishikawa revived the idea of the fishbone diagram to solve problems at the Kawasaki shipyards in the 1960s, and the idea soon caught on. The Fishbone Diagram: A Decades-Old Concept That’s Still Relevant Use it to troubleshoot before there is trouble, and you can overcome all or most of your teething troubles when introducing something new. The fishbone diagram strives to pinpoint everything that’s wrong with current market offerings so that you can develop an innovation that doesn’t have these problems.įinally, the fishbone diagram is also a great way to look for and prevent quality problems before they ever arise. Having a problem-solving product will ensure that your new development will be popular – provided people care about the problem you’re trying to solve. Once all the causes that underlie the problem have been identified, managers can start looking for solutions to ensure that the problem doesn’t become a recurring one.Ĭan also be used in product development. The diagram looks just like a fish’s skeleton with the problem at its head and the causes for the problem feeding into the spine. The fishbone diagram or Ishikawa diagram is a cause-and-effect diagram that helps managers to track down the reasons for imperfections, variations, defects, or failures.
